Applications
Humidity control for the manufacturing industry
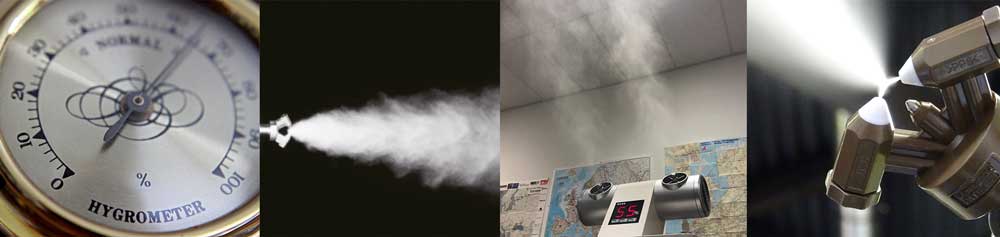
Overview
Humidity control is important for a multitude of industries to have an efficient productivity. To maintain optimal moisture levels is common throughout industrial applications like the food industry, pharmaceutical industry, electronics, printing, diverse manufacturing industries, but also in a niche market like luxurious hospitality industry. Not only is it beneficial for the production process, but also for the well-being and the health of the employees.
Some applications will require dehumidification systems like compressor or desiccant dehumidifiers. Other will require a higher level of humidity like cold rooms for vegetables (above 90% RH with temperatures between 1 – 10°). Depending on the ambient temperatures indoor, the required humidity conditions will vary.
In general, for condensation prevention and optimal humidification effects, it is recommended to have a relative humidity (RH) level between 40 and 60%. But each industrial application has its optimal level of humidity to achieve the best results in productivity.
Issues related to low humidity level and/or no humidity control in production for all types of industries
Nowadays, in the race of constantly producing more and faster while maintaining a good quality level for the products to the end users, manufacturing factories cannot waste time and money in repairs. The production speeds and high-end quality are 2 key factors. However, several issues can occur during the process and damage the products:
- Static electricity damages
- Particle adhesion on end products (product defaults)
- Ignition source / explosion
- Product defects and/or destruction during manufacturing
- Work environment problems caused by low humidity (sick workers) or static charges (electrostatic discharge)
- Dust explosion
- Electric shock to workers and the equipment
- Contamination of components
- Deterioration of the product’s characteristics
- Operation shut down, malfunction of the equipment / machines
- Adhesion and/or repulsion between objects
This generates costs for repairs of the products, cost for the maintenance of damaged machines, costs for the unsold damaged product and creates an unsafe working environment for the operators.
The lack of airborne moisture is the root cause of each of these issues. The dryness of the air enables the generation of static electricity and dust particles to fly around.
That is why onsite management of humidification and temperature conditions became vital for production plants of a multitude of industries. The most popular solutions are steam humidification and water-spray humidification systems.
Solution: Energy-saving systems for humidity control in production
Although steam humidification has been traditionally used in production facilities, in order to lower in-house energy consumption, our solution replaced them. Our humidification system is a water-spray based unit which sprays fine fog. The unit is mounted with pneumatic nozzles which use compressed air and demineralized water.
Water-spray humidification systems do not use fuel oil like steam humidification and in comparison, they use smaller amount of electricity, which reduces the operating costs.
While steam humidification generates heat, our humidity control system sprays non-wetting fog that cools down and humidifies when evaporating in the working environment. This reduces the operating costs of air conditioning. And in consequence, the humidity levels are also accurately controlled and reached as required.
Solutions
Example of Systems / Products used for this application
AirAKI® Industrial humidification system
Humidification units Dry Fog humidifier or Portable humidifier set
- The AKIMist Dry Fog humidifier is part of the AirAKI® system. This humidification unit is recognized as a requirement for soldered electrical and electronic assemblies based on IPC J-STD-001 standard.
IPC standard for IKEUCHI AKIMist
Installed with a controlled panel and humidity sensors, the system offers an effective humidity control in all rooms of the production facility. The humidity sensor will indicate if the system needs to be activated or to stop depending on the excess moisture or lack of humidity in the air. Thanks to the accurate control of the humidity environment, the Dry Fog system offers energy efficiency by reducing the energy cost to 80% of what a tradition steam humidifier would consume.
Benefits
- Accurate control of humidity indoor avoiding both excess of humidity (condensation) and lack of humidity (dryness)
- Solving two problems at once: reducing static electricity and energy costs
- Major energy consumption and operating costs reduction with a lower consumption of electricity
- Cooling and humidifying without wetting the environment, the objects, and the workers
- Facilitate production speeds and quality by controlling the product end results, the humidity-and temperature level.
Related articles about humidifiers and the importance of humidity:
- Type of humidifiers: what’s on the market?
- What is the difference between relative and absolute humidity?
- Factors that affect the control of the humidity and its level
- Effect of lack of humidity
- The right humidity level for each industry
- How can you calculate the required amount of humidification for your factory?
- Dry Fog introduction
- Benefits of a Dry Fog
- The results of Dry Fog in different industries